Your Strategic Partner for
Unlocking China's Sourcing Potential
Purchase skills | When visit the supplier, what to see at the production site?
On-site observation is often due to time constraints, and buyers need to be sharp-eyed and make quick assessments and judgments on the spot in a short time. This article does a preliminary discussion on the topic of what to see at the production site.
The importance of on-site observation
On-site observation is the basis for continuous improvement. Toyotaโs Naiichi Ohno has achieved the ultimate in on-site observation. Even on factory holidays, he will bring management personnel to the site, let people stand in the workshop and observe quietly for half an hour, and then point out areas for improvement. Only in this way can we truly achieve endless improvement and achieve the PDCA cycle.
People in this company often turn a blind eye to many problems, or think that these small problems are harmless, or think that they cannot be changed. There are also many managers who tend to turn a blind eye to intuitive information and only focus on output. As a result, some key clues may be ignored, and the real situation of the enterprise may not be truly understood.
As customers, we should go to the supplierโs site to understand its cost structure, production efficiency, and quality control.
Enterprise operation is a large system, all links are closely related and affect each other. For production-oriented enterprises, you can know the details through any details on the scene. Any major problem can be found on the spot. Even in a limited time, as long as you grasp the key points, you can fully grasp the key information about the operation of the factory. Letโs talk about how to conduct on-site observation.
1. Atmosphere
At the scene, you can first intuitively see the truest mental outlook of employees. There will be a sharp contrast between passionate employees and indifferent employees. Because these directly reflect the emotions of workers and their satisfaction with the factory. In a factory I visited, workshops were playing cheerful music. At a glance, the workers were very enthusiastic about labor. Working in such a relaxed and pleasant environment, the efficiency is relatively higher, and the quality of the products will also make people feel better. More confident.
In the workshop, you can pay attention to observe whether there is unevenness of busyness and idleness. For example, when the machine is automatically processing, workers are idle for a long time, or workers at some stations are waiting for materials for a long time. The existence of this phenomenon indicates that the factory lacks management, the utilization rate of personnel is low, and idle employees will also affect the working atmosphere of other people. The overall work efficiency is low and the cost is bound to be higher.
You should also pay attention to whether the workshopโs light is sufficient, the air circulation is smooth, whether there is a peculiar smell, whether there is too much noise, and whether the workshop is tidy, because these will directly affect the mood of the workers, and then affect the production efficiency and product quality.
It is hard to imagine that a factory with a lazy on-site atmosphere and depressed employees can make good products.
2. Space utilization and layout
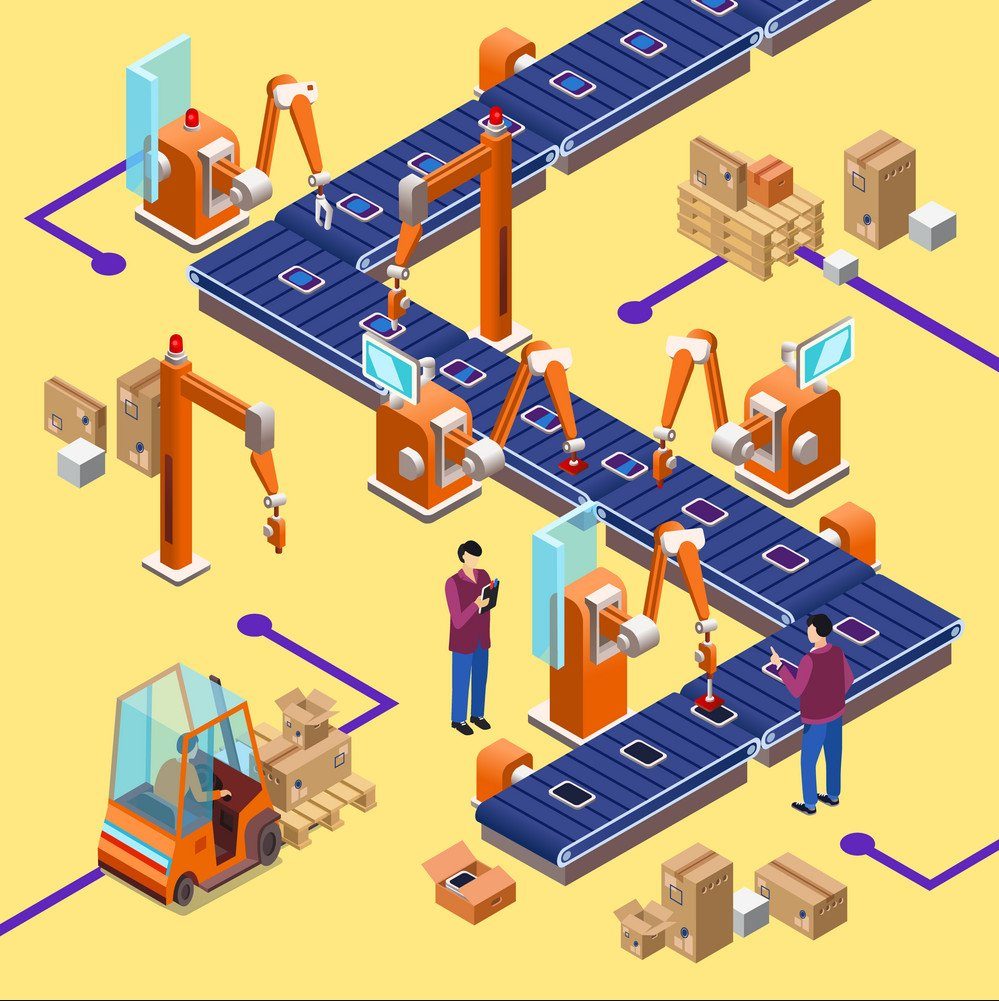
movement of goods
Many factories in China are crave for greatness and success. They think the bigger the production workshop, the better. As a result, the utilization rate is often very low. The equipment and process layout are scattered. In addition to wasting space, materials are also needlessly moved in the factory.
Transportation tools not only occupy space, have high operating costs, but also cause unnecessary material movement. I saw a lot of electric forklifts shuttle busily in a factory, but there was a lot of unnecessary transportation among them. For example, after the same batch of parts are moved from area A to area B for processing, they are moved back to area A for subsequent processing, then moved to area C for processing, and finally moved back to the warehouse of area B.
In principle, the production materials used on the day should be stored along the production line instead of being stored separately in several storage areas. Tools and tooling should be placed as close to the machine as possible. The layout of the factory should ensure the smooth flow of products and try to avoid any partitions.
3. On-site standardization
Standards are the best state and unified implementation reference. Without standards, there is no implementation, and there is no focus on improvement. There should be many standards at the production site, including operation and quality standards, 5S and safety standards, operation and maintenance standards, process and rework standards, safety stock standards, and so on.
By observing the specific operation process of different employees in the same process, you can find out whether there are differences, including the sequence of actions, the intensity of operations, and whether there are omissions. Differences indicate that employees lack standardized operation training, which greatly increases the possibility of product defects. When I visited a supplierโs factory, I found that different workers lock the four screws in a different order, and there is no standard torque reference. Some workers will lock it twice, and some will only lock it once. No wonder the screws fall off and customers complain.
4. Quality Control
On-site observation should focus on how the workshop handles defective products. A good factory will expose the problem instead of covering up defective products and waste. For example, use a red label to highlight it, so that you can immediately know whether waste is increasing or whether a certain part of the production process is producing defective products.
I saw a lot of defective products in a corner of a factory. From the dust on it, it can be seen that they have accumulated for a long time, but there is no sign to explain the reason and problem of the defect. Who dares to cooperate with a factory with such chaotic quality management?
In a good factory, each component has a card or a document to follow the circulation, indicating the source, the processing personnel, the equipment used and other information. Any problem found in any process can be easily traced to the source, which is also convenient improve.
5. Visualization
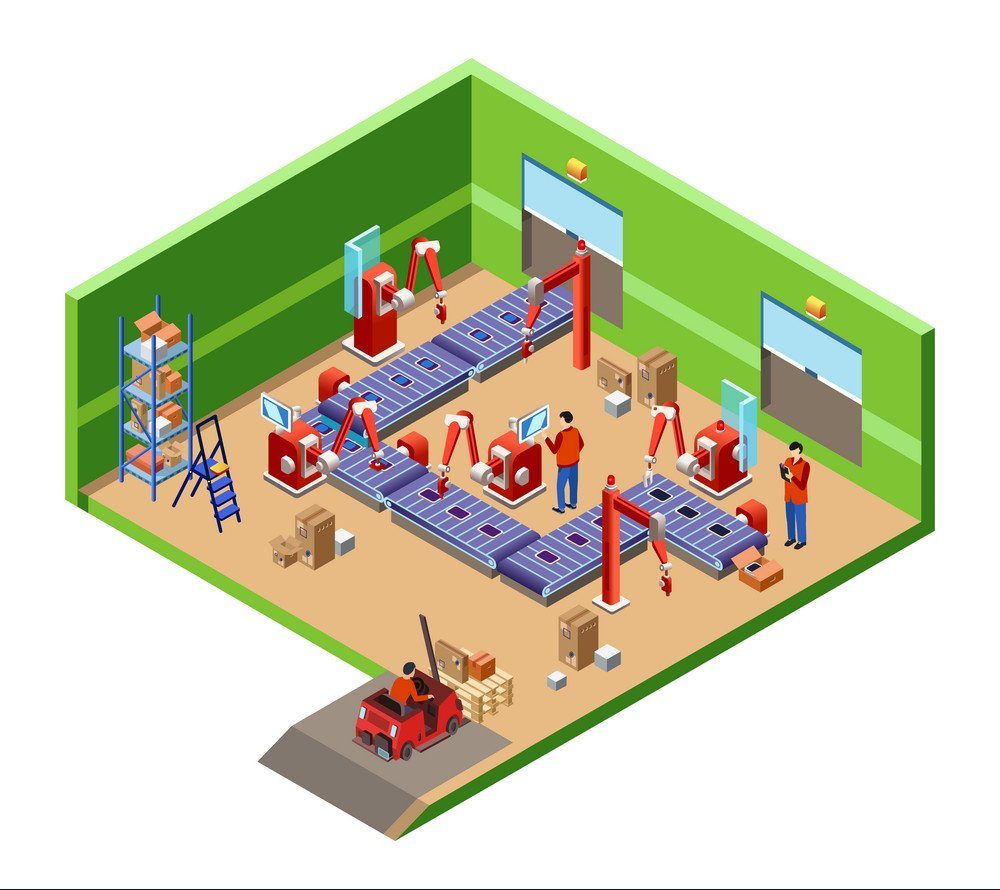
factory inspection
Visual management is the basis of many advanced management methods, and it is an intuitive communication of the management level of a manufacturing enterprise. In a well-managed factory, visual tools are everywhere. Including the organization and standardization of the workplace, the visualization of result indicators, the visualization of standard operations, the visualization of control indicators, the visualization of automatic error prevention and correction, and the alarm mechanism. When visiting, you should look for various visual tools.
The visual management blackboard can be divided into static and dynamic management blackboards. The static blackboard mainly conveys the long-term management philosophy of the organization, and the dynamic blackboard is the management information that managers must grasp at any time, and can better reflect the management level and ability of a factory.
A lot of promotional slogans are hung in many factories and workshops I have seen, and the boss is proud to show off the corporate culture. Visualization is done well, but these factories rarely use dynamic blackboards, or the data information on dynamic blackboards has not been updated for several months. This shows that the blackboard has no practical effect at all.
For example, in a large motor manufacturing plant, the production workshop is almost spotless at a glance. All the floors are painted with beautiful paint. Various visual lines and signs are all made to look beautiful, but there is only a lack of safety warning signs. . If the road surface is too smooth, there is insufficient friction, and people will slip and fall if they walk on it. This superficial effort is sufficient, but there are still many security risks.
6. Equipment status
In a good factory, the equipment is clean and well maintained, and the equipment-related information is clear and updated instantly. In the processing workshop of a foundry, although the various lathes are not very advanced and even have a long history, they are all operating in good condition. I saw a card visibly posted on the side of each machine, which recorded the model, purchase date, price, supplier, repair records, maintenance records, etc. of the equipment. In addition, the daily checklist is also very complete. Some checklists clearly record the hidden dangers discovered by the operator, as well as the signature and handling plan of the equipment department. This shows that equipment management and maintenance have formed a benign system.
On-site observation is the most direct way to discover problems. Most of the problems will be manifested on-site. A preliminary assessment of the factory can be made quickly, and the root cause can be traced to reduce the blindness of a lot of work.